NASA-TM-110309
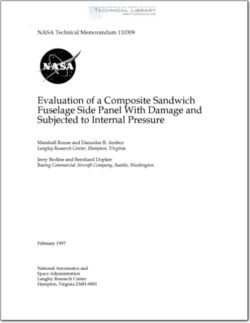
- Version
- 152 Downloads
- 698.49 KB File Size
- 1 File Count
- April 6, 2016 Create Date
- April 6, 2016 Last Updated
Evaluation of a Composite Sandwich Fuselage Side Panel with Damage and Subjected to Internal Pressure
The results from an experimental and analytical study of a composite sandwich
fuselage side panel for a transport aircraft are presented. The panel has two window
cutouts and three frames, and has been evaluated with internal pressure loads that
generete biaxial tension loading conditions. Design limit load and design ultimate
load tests have been performed on the graphite-epoxy sandwich panel with the middle
frame removed to demonstrate the suitability of this two-frame design for supporting
the prescribed biaxial loading conditions with twice the initial frame spacing of 20
inches. The two-frame panel was damaged by cutting a notch that originates at the
edge of a cutout and extends in the panel hoop direction through the window-belt
area. This panel with a notch was tested in a combined-load condition to demonstrate
the structural damage tolerance at the design limit load condition. The two panel
configurations successfully satisfied all desired load requirements in the experimental
part of the study, and the three-frame and two-frame panel responses are fully
explained by the analysis results. The results of this study suggest that there is
potential for using sandwich structural concepts with greater than the usual 20-in.-wide
frame spacing to further reduce aircraft fuselage structural weight.
The potential for cost and weight reduction offered by composite-facesheet
sandwich structures in aircraft fuselage side panels is currently being investigated in
the NASA Advanced Composite Technology Program. Structural trade studies for
sandwich concepts that use advanced material placement methods, such as tow
placement for skin and three-dimensional braiding for frames, have identified a 25
percent cost and weight reduction compared to conventional integrally-stiffened
metallic structures (Ref. 1). Sandwich structures offer additional potential for weight
reduction by decreasing the number of frames by increasing the fuselage frame
spacing. Sandwich structures are good candidates for implementing greater frame
spacing than the usual 20 to 22 in. frame spacing since skin panels for these
structures have much higher bending stiffnesses than the more conventional stringer-
frame stiffened skins with minimum gauge thicknesses. The sandwich panel
described in the present paper has been designed to generate preliminary
performance information for sandwich structures with twice the usual fuselage frame
spacmg.
File | Action |
---|---|
NASA-TM-110309 Evaluation of a Composite Sandwich Fuselage Side Panel with Damage and Subjected to Internal Pressure.pdf | Download |
Comment On This Post