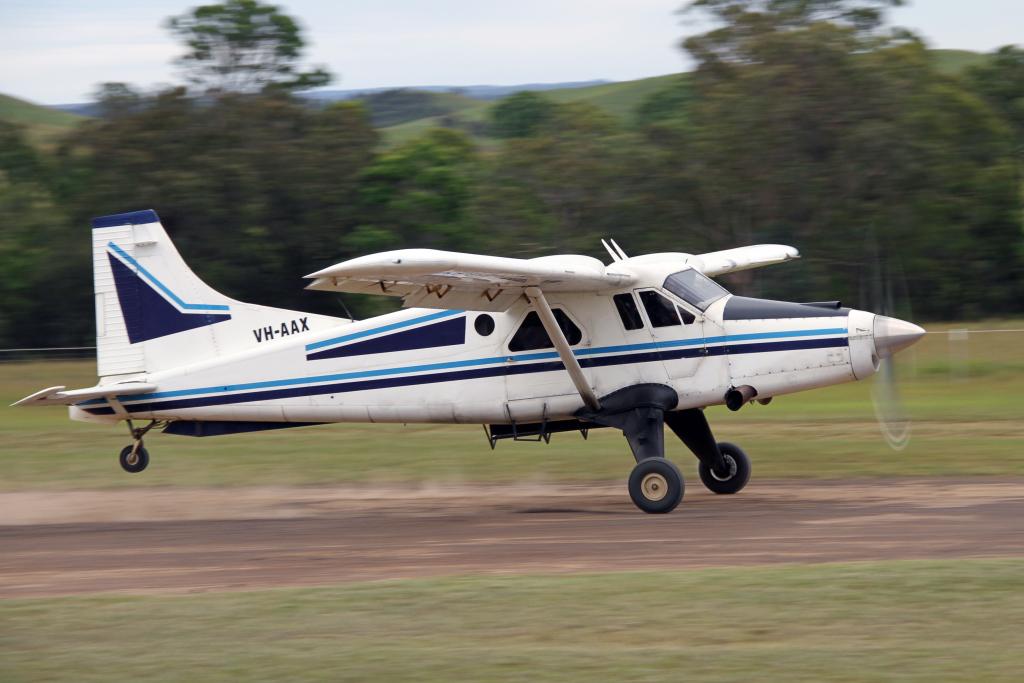
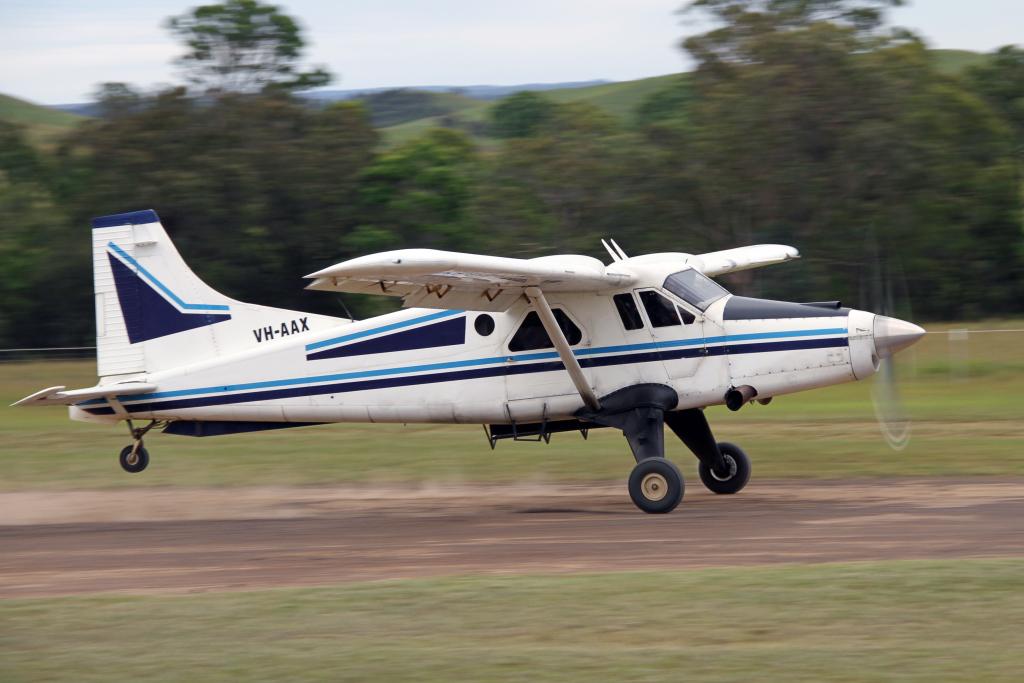
On 4 April 2022, the pilot of a de Havilland Canada DHC-2/A1 Beaver aircraft, registered VH-AAX, was conducting parachute flights overhead Moruya Airport, New South Wales. Shortly after the parachutists had exited the aircraft, the pilot heard a loud bang and experienced vibrations as the engine failed.
Believing the aircraft had experienced an engine failure, the pilot pulled the fuel emergency shut-off lever, feathered the propeller, assessed the position of the parachutists, and conducted a forced landing at Moruya Airport.
A post-flight examination of the aircraft identified holes in the cowling above the engine compartment, perforation of the external wall of the engine combustion chamber, holes through the exhaust assembly, and significant damage to the turbine section.
Categorized as "Serious Incident" , the ATSB investigation established that errors by a previous maintainer of the aircraft when determining the engine operating cycles and engine component total equivalent cycles meant that the 3rd-stage turbine wheel remained in-service beyond the component life-limit.
ATSB Director Transport Safety Kerri Hughes said ,
“A post-flight examination of the aircraft identified holes in the cowling above the engine compartment, perforation of the external wall of the engine combustion chamber, holes through the exhaust assembly, and significant damage to the turbine section,”
“A low-cycle fatigue crack had initiated in the 3rd-stage turbine wheel of the Honeywell International TPE331 engine and grown to failure.”
Errors made by a previous maintainer when determining the engine operating cycles and total equivalent cycles accrued by engine components resulted in the 3rd-stage turbine wheel remaining in-service beyond the component life-limit.
In addition, the ATSB established that the operator had estimated the number of engine shutdowns conducted each day based on recollection only. This increased the likelihood that the recorded cycles were incorrect. The ATSB was unable to determine if this resulted in any errors.
The engine was transported to a Honeywell facility in the United States for a teardown and detailed examination supervised by the National Transportation Safety Board.
The examination found that :
Both Honeywell and the National Transportation Safety Board concluded that the most likely reason for the engine failure was a low-cycle fatigue failure of the 3rd-stage turbine wheel.
When a low-cycle fatigue crack on the 3rd-stage turbine wheel, grew to a critical size, a fragment of the wheel was liberated under load, which initiated the engine failure. The fragment impacted the combustion case and became lodged.
The separation of this wheel fragment resulted in significant rotational imbalance, which led to fracturing of the main and torsion shafts. Detached turbine section components then exited the engine, damaging the exhaust assembly.
There was no evidence that any turbine wheel fragments exited through the combustion case with sufficient energy to cause a hazard to the aircraft. As such, the failure was deemed to be contained.
“This incident highlights the critical importance of accurate records of equivalent cycles accrued by an engine and engine components,” said Ms Hughes.
“Cycles should be diligently recorded, calculated, and checked to ensure the equivalent cycles accrued by a component is known with confidence.
“This means that components can be replaced prior to the published in-service life-limit being reached.”
On 9 August 2006, the United States Federal Aviation Administration issued airworthiness directive (AD) 2006-14-03, applicable to Honeywell TPE331 series turboprop and TSE331-3U model turboshaft engines.
The AD was issued to prevent an uncontained engine failure resulting from fracturing of the turbine rotor due to low-cycle fatigue. This AD was developed in response to several reports of uncontained turbine rotor separation that had resulted in metal fragments either penetrating the engine case or exiting the tail pipe, on engines used in ‘special-use’ operations.
Special-use operations was defined as those aircraft that make multiple take-offs and landings without an engine shutdown, such as parachute and agricultural spraying operations. The additional take-offs and landings result in the life-limited parts accruing low-cycle fatigue damage at a faster rate when compared with passenger and freight transport flights.
Display Picture : Dr Ron Report Source : ATSB AO-2022-025